Craftsman Ernie Navarre leaned over a pear-shaped shaped piece of wood. It is the front of what will become an acoustic guitar.
“I’m making sure that the center is true and it's where it should be,” Navarre said.
Navarre is getting ready to install a decorative inlay that adds a little flair to one of Taylor’s acoustic guitars. A router has already carved out a patterned groove and Navarre will fill that with strips of leather called purflings.
The decoration gives a visually pleasing flare to the Taylor Guitars builder’s edition.
Inserting the eye-pleasing trim requires careful placement, sanding and most of all, patience. The job is done by hand for every guitar.
Navarre works at Taylor’s El Cajon factory. The complex is a nondescript collection of office park buildings which serve as both headquarters and factory.
Here is where all the cutting, bending, gluing and polishing are done so select stocks of wood can become the firm’s trademarked guitars.
Wood plays an important role
Chris Wellons is the vice president of manufacturing at Taylor Guitars and on this day he was walking around the plant in jeans and an untucked blue shirt.
“What are you working on?” Wellons asked a co-worker hunched in front of a computer screen. After a brief exchange, the Taylor executive moves on.
In many ways, this is Wellon’s building. He is responsible for maintaining a perfect environment for woodworking in this sprawling facility.
“What we’re trying to do with the wood is get it to a certain moisture content and percentage rate throughout the factory. We want the guitar to be stable as we build the guitar,” Wellon said.
His challenge is to keep environmental conditions stable inside the building so the wood isn’t constantly expanding and contracting which changing temperature and moisture conditions in the air.
Changing conditions can spoil efforts to build a high-quality wood instrument.
And high quality is what company officials depend upon, especially master builder Andy Powers.
“I started when I was a kid. I got really, really interested in guitars. And so I started building instruments and playing them,” Powers said.
“In the beginning, I got a piece of ebony, I made a guitar. I was a guitar maker. But now I’m more than that. Where is the wood going to come from, 50 years from now, 100 years from now?” – co-founder and president Bob Taylor
His design work is realized on the production floor, but he spends a lot of time sketching the future at his office’s drawing table.
The decidedly low-tech sketchbook and pencil help him work through design ideas that end up in the guitars that carry the Taylor brand.
Wood plays a critical role.
“A lot of other things are too stiff, not stiff enough. They’re too resonate. Or not resonate enough. It’s like there’s too much of something. But woods have such a unique variety of characteristics. You can choose a material that works exactly right for each part of the guitar,” Powers said.
And one key part of the guitar that requires a special kind of wood is the fingerboard. It sits just under the strings on the guitar’s long neck. And the fingerboard on Taylor guitars is made of ebony, a wood so dense it doesn’t float.
“This part doesn’t get finished over with any lacquers or coatings of any kind. It’s just left as raw wood. So you need something really dense and hard that doesn’t wear away,” Powers said.
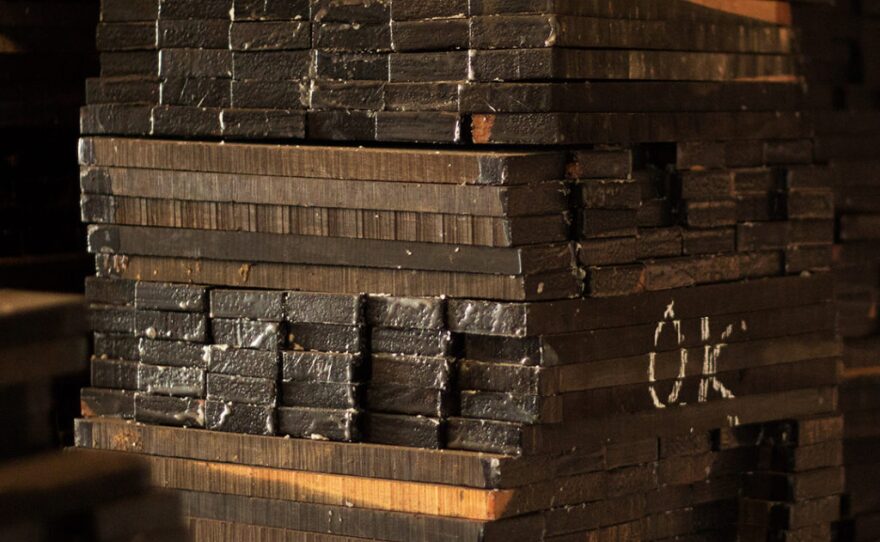
But Ebony only grows in a few tropical regions and there is competition for the dwindling resource.
Ebony is getting harder to find
Just going out and finding ebony on the market is no longer enough.
American guitar-maker Gibson was fined hundreds of thousands of dollars a few years ago for possessing illegally obtained ebony. That wood was harvested in a restricted area.
Taylor Guitars decided to secure a piece of the company’s future by buying a lumber mill in Cameroon. The mill included permits to harvest local ebony trees that will eventually wind-up as parts for the firm’s acoustic instruments.
But there was more to do, said Taylor as he looked down pensively at one of his company’s guitars.
RELATED: Taylor Guitars Still Strumming Along As Example Of San Diego Manufacturing Success
“In the beginning, I got a piece of ebony, I made a guitar. I was a guitar maker. But now I’m more than that,” said company co-founder and president Bob Taylor.
“Where is the wood going to come from, 50 years from now, 100 years from now?” Taylor asked.
The company uses about 300 ebony trees a year and part of the firm’s ebony sustainability project involves replanting the tropical trees.
Taylor’s goal is to leave behind 500 young trees for every one the company cuts down.
Taylor is also seeking out landowners with mature ebony trees.
“We go onto a private owners' land, and we say you have dead and dying trees in here. And we’re talking about trees, if they were people, would all be on walkers and an oxygen tank. We can take these out and the value that we get out of the good wood, we will reforest your land,” Taylor said.
That sales pitch includes a pitch for the future. Allow the guitar maker to cut down the old mature trees and the firm will replant the land with ebony sprouts.
Taylor is asking landlords to be patient because it takes ebony trees 60 to 200 years before they mature and the guitar industry can only use wood from fully grown trees.
“All this effort that’s going on in Africa right now, in Cameroon, is for one piece of the guitar. It’s not for the guitar. It’s one little piece that costs $5,” Taylor said.
But that $5 piece of wood is crucial and the effort to preserve access to the dark and dense hardwood may become part of the cost of doing business for guitar makers like Taylor.
High-quality raw materials are essential for a firm that sells quality as part of its brand.